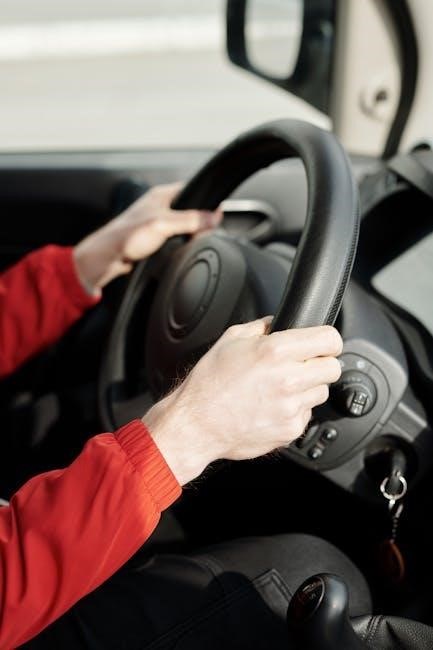
The Honeywell Burner Control Manual PDF provides comprehensive guidance for installing, operating, and maintaining burner control systems, ensuring safety and efficiency in industrial combustion processes.
1.1 Overview of Honeywell Burner Controls
Honeywell burner controls are advanced, microprocessor-based systems designed for safe and efficient operation of industrial combustion equipment. These controls integrate flame supervision, ignition, and fuel valve management, ensuring reliable performance for gas, oil, or combination fuel burners. The RM7890A,B,C series, for example, offers enhanced diagnostics, programmable settings, and remote monitoring capabilities, making them ideal for modern industrial applications. They combine robust safety features with user-friendly interfaces to optimize burner operation and maintenance.
1.2 Importance of the Manual for Installation and Operation
The Honeywell Burner Control Manual is essential for proper installation, operation, and maintenance of burner systems. It provides detailed instructions, safety protocols, and technical specifications to ensure compliance with industry standards. The manual includes troubleshooting guides, wiring diagrams, and operational sequences, making it a critical resource for technicians and operators. Adhering to the manual’s guidelines minimizes risks, ensures efficient performance, and prolongs the lifespan of the burner control system.
Key Features of Honeywell Burner Control Systems
Honeywell burner control systems offer advanced safety mechanisms, programmable settings, and real-time diagnostics, ensuring reliable operation, efficiency, and compliance with industry standards.
2.1 Microprocessor-Based Integrated Burner Controls
The Honeywell RM7890 series employs microprocessor-based technology, providing advanced burner control with features like automatic sequencing, flame supervision, and system diagnostics. These controls integrate seamlessly with various fuel types and offer programmable options for tailored performance. Enhanced safety is ensured through continuous monitoring and self-diagnostics, making them ideal for industrial applications requiring precise and reliable combustion management. The system’s non-volatile memory retains operational history, aiding in troubleshooting and maintenance efficiency.
2.2 Safety Provisions and Functional Capabilities
Honeywell burner controls incorporate advanced safety provisions, such as flame supervision, lockout mechanisms, and fault history logging, to ensure reliable and secure operation. These systems are designed to prevent accidents by continuously monitoring burner performance and shutting down operations if unsafe conditions arise. Functional capabilities include programmable sequences, real-time diagnostics, and customizable settings, allowing for precise control and adaptability in various industrial applications. These features enhance both safety and operational efficiency, making Honeywell controls a robust solution for combustion systems.
2.3 Programmable Features and Diagnostics
Honeywell burner controls offer programmable features that allow customization of burner sequences, timing, and operational parameters. Advanced diagnostics provide real-time monitoring and fault detection, enabling quick identification and resolution of issues. The system stores historical data on faults, including timestamps and operational statuses, aiding in troubleshooting and maintenance. Programmable relight or lockout options enhance flexibility, while nonvolatile memory ensures settings and histories are retained even during power outages, optimizing system reliability and performance.
Safety Precautions and Guidelines
Adhering to safety protocols is crucial when handling Honeywell burner controls. Ensure all fuel valves are closed during installation, and follow proper wiring procedures to prevent hazards and ensure reliable operation.
3.1 General Safety Instructions
Always ensure manual fuel shutoff valves are closed before starting installation or maintenance. Properly connect all electrical and fuel components to avoid hazards. Use appropriate flame detectors and ensure they are clean and correctly installed. Regularly inspect wiring and connections for damage or wear. Avoid exposing the control unit to extreme temperatures or moisture. Follow all safety protocols outlined in the manual to prevent accidents and ensure reliable burner operation. Adhere to local safety regulations and guidelines when working with combustion systems.
3.2 Electrical and Fuel Safety Considerations
Ensure all electrical connections are secure and meet local codes to prevent arcing or shorts. Use appropriate flame detectors and verify their compatibility with fuel types. Maintain proper fuel line pressure and purge systems before ignition; Install surge protectors to safeguard against voltage spikes. Keep the area well-ventilated to prevent gas accumulation. Regularly inspect fuel valves and actuators for leaks or damage. Follow grounding procedures to eliminate static electricity risks. Always use Honeywell-approved components for reliable operation and safety.
Installation Requirements
Ensure proper grounding, correct mounting of the relay module, and compatibility of components. Verify all electrical connections and fuel line setups meet safety standards and system specifications.
4.1 Pre-Installation Checks
Begin by verifying all components are undamaged and compatible. Check fuel type compatibility and electrical ratings. Ensure the system meets local safety regulations. Review the manual for specific requirements. Inspect wiring and connections for integrity. Confirm the correct mounting orientation and space allocation. Validate the availability of necessary tools and documentation. Ensure all safety precautions are understood and followed to prevent installation errors and potential hazards.
4.2 Mounting the Relay Module and Subbase
Mount the RM7890 relay module and Q7800 subbase securely in a vertical or horizontal orientation, ensuring easy access for maintenance. Use the provided mounting hardware and follow dimensional guidelines from the manual. Ensure the module is installed in a dry, cool environment, away from direct sunlight and moisture. Proper alignment and secure fastening are crucial for reliable operation and to prevent vibration damage. Refer to the installation diagram for precise measurements and placement.
4.3 Assembly of Components
Assemble the RM7890 system by attaching the relay module to the subbase and connecting optional components like the Keyboard Display Module. Ensure all plug-in flame amplifiers and detectors are securely fitted. Connect wiring carefully, following the diagram to avoid mismatches. Verify that all sensors, such as flame rods and photocells, are properly aligned and installed. Tighten all connections firmly to prevent loose contacts, which could cause system malfunction. Refer to the manual for specific torque specifications and assembly sequences.
Wiring and Connections
Ensure proper wiring of the RM7890 system, following the provided diagrams. Connect flame detectors, fuel valves, and ignition components securely. Verify all terminals and voltage levels match specifications for safe and efficient operation.
5.1 Main Power and Signal Wiring
Connect the main power supply to the designated L1 and L2 terminals, ensuring proper grounding for safety. Wire the signal connections according to the manual’s diagrams to prevent misconfiguration. Verify that all terminals are securely fastened and voltage levels match the specifications provided. Proper wiring ensures reliable communication between components and prevents potential hazards. Always refer to the manual for precise instructions and diagrams to guarantee accurate installation and operation of the burner control system.
5.2 Flame Detector and Ignition Wiring
Connect the flame detector to the designated terminals, ensuring correct polarity for proper signal transmission. Wire the ignition electrodes to the control module, maintaining the specified voltage to prevent misfires. Secure all connections to avoid loose wires, which could disrupt flame detection. Use shielded cables for signal integrity, especially in noisy environments. Follow the manual’s wiring diagrams precisely to ensure reliable flame detection and ignition, critical for safe burner operation and system efficiency.
5.3 Fuel Valve and Actuator Connections
Connect the fuel valve to the burner control module, ensuring proper wiring to the designated terminals. Use the appropriate actuator type specified in the manual for smooth operation. Verify the voltage rating matches the system requirements to prevent damage. Refer to the wiring diagram for correct connections between the actuator, fuel valve, and control module. Test the connections to ensure the valve opens and closes as commanded, ensuring reliable fuel flow and system efficiency.
Operational Sequences
The Honeywell Burner Control system operates through predefined sequences, ensuring smooth startup, steady operation, and safe shutdown. These sequences integrate safety checks, monitoring, and lockout conditions for reliable performance.
6.1 Startup and Shutdown Procedures
The Honeywell Burner Control system follows detailed startup and shutdown procedures to ensure safe and efficient operation. Startup begins with a pre-purge cycle, followed by pilot ignition and main burner activation. Shutdown procedures include a post-purge phase to clear residual fuel. The system monitors flame presence and fuel flow, automatically locking out if unsafe conditions arise. LEDs provide visual feedback, and the manual outlines troubleshooting steps for common issues, ensuring smooth transitions between operational states while maintaining safety protocols. Proper sequential shutdown prevents residual fuel ignition risks.
6.2 Normal Operation and Monitoring
During normal operation, the Honeywell Burner Control system ensures smooth fuel and air regulation, adjusting to load demands while maintaining consistent combustion. The system continuously monitors flame presence, fuel flow, and safety parameters. Diagnostics and status LEDs provide real-time feedback, enabling quick identification of operational issues. The control module logs performance data, aiding in predictive maintenance. Monitoring tools include remote access options, allowing operators to track system status and receive alerts for alarms or deviations from setpoints, ensuring optimal performance and safety.
6.3 Emergency Shutdown and Lockout Conditions
The Honeywell Burner Control system is designed to automatically shut down and lock out in emergency situations, such as loss of flame detection, low fuel pressure, or system faults. These conditions trigger a fail-safe mode to prevent hazardous situations. The control module logs the cause of the lockout, providing clear diagnostics for troubleshooting. Resetting the system requires addressing the root cause and following specified reset procedures to ensure safe and reliable operation.
Diagnostics and Troubleshooting
The Honeywell Burner Control system features advanced diagnostics, using LEDs and fault codes to identify issues quickly. Troubleshooting guides help resolve common problems efficiently, ensuring system reliability.
7.1 Understanding Fault Codes and LEDs
The Honeywell Burner Control system utilizes fault codes and LED indicators to simplify troubleshooting. LEDs provide visual status updates, while fault codes offer detailed error information. These tools help identify issues like flame failures or system lockouts. The manual includes a comprehensive list of codes, their meanings, and corresponding LED sequences, enabling technicians to diagnose and resolve problems efficiently, ensuring minimal downtime and optimal system performance.
7.2 Troubleshooting Common Issues
Troubleshooting common issues with Honeywell Burner Controls involves systematic checks of ignition, fuel flow, and system responses. The manual provides step-by-step guides to address frequent problems like faulty flame detection, gas valve malfunctions, or ignition failures. By referencing fault codes and LED indicators, technicians can pinpoint the root cause. Additionally, the manual offers solutions such as resetting the system or replacing components, ensuring quick resolution and restoring burner operation efficiently. Regular maintenance practices are also emphasized to prevent recurring issues.
7.3 Resetting the System After a Lockout
After a lockout, resetting the Honeywell Burner Control System involves specific steps to ensure safe and proper operation. First, allow the burner to cool down completely. Verify that all safety conditions are met and the cause of the lockout has been resolved. Close the manual fuel valve, then press and hold the reset button for 5-10 seconds. Release the button and slowly open the fuel valve. The system will automatically restart if no issues persist. Some models may require a 30-minute wait after a lockout before resetting. Always refer to the manual for model-specific instructions.
Maintenance and Service
Regular maintenance ensures optimal performance and safety of Honeywell Burner Control Systems. This includes routine checks, component replacements, and diagnostics to maintain efficiency and reliability over time.
8.1 Routine Maintenance Tasks
Regular maintenance involves inspecting flame detectors, cleaning sensors, and verifying proper electrical connections. Additionally, checking fuel valve operation and ensuring all components are free from debris is essential. Scheduled maintenance prevents premature wear and ensures the burner control system operates safely and efficiently. Always refer to the Honeywell manual for specific tasks and intervals to maintain system integrity and performance;
8.2 Replacing Components and Upgrades
Replacing components such as flame detectors or amplifiers requires adherence to Honeywell’s guidelines to ensure compatibility and safety. Upgrades may involve installing new software or hardware modules to enhance functionality. Always use genuine Honeywell parts to maintain system reliability. Before performing any replacement or upgrade, power down the system and follow the manual’s step-by-step instructions to avoid errors and potential hazards.
8.3 Calibration and Adjustment Procedures
Calibration ensures optimal performance and safety of Honeywell burner controls. Adjustments may involve setting fuel ratios or timing sequences. Use diagnostic tools to verify flame signals and system responses. Follow the manual’s detailed calibration steps, ensuring all parameters align with manufacturer specifications. Regular adjustments prevent operational inefficiencies and potential hazards, maintaining compliance with safety standards and extending equipment lifespan.
Technical Specifications
Honeywell burner control systems are designed for gas, oil, or combination fuels, operating within specified voltage ranges and environmental conditions to ensure reliable performance and safety.
9.1 Electrical Ratings and Compatibility
Honeywell burner control systems are designed to operate within specified electrical ratings, ensuring compatibility with various power supplies. They typically support voltage ranges of 100-240VAC at 50/60Hz, accommodating single-phase and three-phase configurations. These systems are UL and CE certified, adhering to international safety standards. Compatibility with diverse electrical systems ensures reliable performance across different industrial environments. Proper installation within rated specifications guarantees safe and efficient operation, minimizing risks of electrical faults or system malfunctions. Always refer to the manual for precise electrical requirements and compliance guidelines.
9.2 Fuel Types and Application Limits
Honeywell burner controls are compatible with various fuel types, including natural gas, propane, oil, and combination fuels. These systems are designed for single-burner applications, ensuring reliable operation across diverse industrial and commercial settings. Application limits include specific temperature ranges, fuel pressure requirements, and burner capacities, all detailed in the manual to ensure optimal performance and safety. Proper fuel type selection and adherence to specified limits are crucial for efficient and safe burner operation. Always consult the manual for fuel-specific guidelines and compatibility.
9.3 Environmental and Operating Conditions
Honeywell burner controls are designed to operate within specific environmental conditions, including temperature ranges of -20°C to 60°C (-4°F to 140°F) and relative humidity up to 90%. They are suitable for industrial environments and must be protected from dust, chemicals, and excessive vibrations. Operating conditions include compatible power supply voltages, such as 120V or 230V AC, and frequency requirements. The systems are built to withstand typical industrial environmental challenges while maintaining reliable performance and safety standards.
Annexures and References
The manual includes annexures with additional resources, contact information, and a glossary for troubleshooting guides and technical support references.
10;1 Glossary of Terms
This section provides a detailed glossary of technical terms related to Honeywell burner controls, ensuring clarity for users. It defines key concepts like “flame safeguard,” “ignition trial,” and “lockout,” aiding in troubleshooting and system operation. The glossary serves as a quick reference for understanding complex terminology used throughout the manual, making it essential for technicians and operators to ensure safe and effective burner control system management.
10.2 Additional Resources and Contact Information
For further assistance, this section offers additional resources, including technical guides, FAQs, and Honeywell’s customer support details. Contact information for regional offices and authorized distributors is provided to address specific queries or troubleshooting needs. Online forums and training materials are also highlighted, ensuring users have access to comprehensive support for optimal burner control system performance and maintenance.