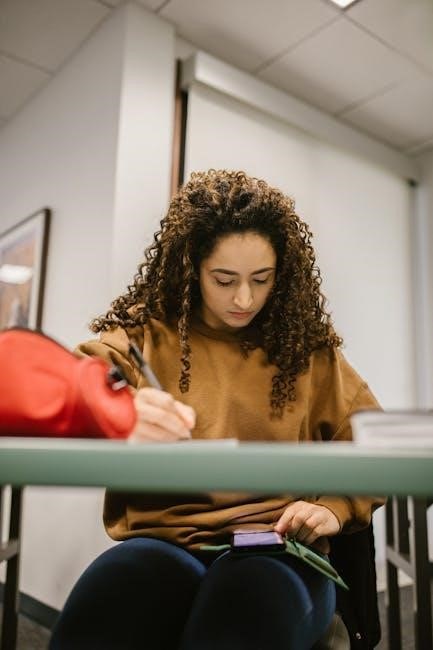
This resource provides a comprehensive guide to manual handling quiz questions and answers, offering multiple-choice and true/false options. It covers key topics like proper lifting techniques, employer responsibilities, and injury prevention strategies. The quiz is designed to test knowledge and ensure compliance with safety regulations, making it an essential tool for both employees and employers.
What is Manual Handling?
Manual handling refers to any activity that involves lifting, lowering, pushing, pulling, carrying, or moving objects or people. It is a common task in many industries, including healthcare, manufacturing, and construction. Proper manual handling techniques are essential to prevent injuries and ensure workplace safety. The goal of manual handling is to minimize strain on the body, particularly the back, by using correct postures and methods. Understanding the principles of manual handling is crucial for both employees and employers to create a safer working environment. This section provides a clear definition and explains the importance of safe practices in everyday operations.
Why Manual Handling Training is Important
Manual handling training is crucial for reducing workplace injuries and promoting a culture of safety. It equips employees with the knowledge and skills to perform tasks safely, minimizing the risk of musculoskeletal disorders. Proper training ensures compliance with legal requirements and industry standards, protecting both workers and employers. By understanding correct lifting techniques, employees can avoid common hazards and maintain a healthy work environment. Additionally, manual handling training fosters awareness of employer responsibilities and the importance of risk assessments. Regular training and quizzes help reinforce these principles, ensuring a safer and more efficient workplace for everyone involved.
Benefits of Using Quizzes for Manual Handling Training
Quizzes are an effective tool for reinforcing manual handling training by engaging employees and assessing their understanding. They help identify knowledge gaps, ensuring workers can apply safe practices. Regular quizzes promote active participation and long-term retention of safety protocols. Interactive formats make learning enjoyable, fostering a culture of safety. Quizzes also provide immediate feedback, allowing for timely corrections. By testing knowledge, quizzes ensure compliance with legal standards and reduce workplace injuries. They are a valuable addition to training programs, enhancing overall safety and efficiency in the workplace. Regular testing helps maintain a high level of awareness and adherence to manual handling best practices.
Key Principles of Manual Handling
Key principles include assessing tasks for risks, using proper lifting techniques, and minimizing manual handling when possible. Training, ergonomics, and load management are also crucial for safety and efficiency.
Definition and Scope of Manual Handling
Manual handling refers to any activity that involves lifting, carrying, pushing, pulling, or moving loads. It spans various industries, including healthcare, manufacturing, and construction. The scope includes tasks that require physical effort, posing risks of injury. Proper techniques and regulations aim to minimize strain and prevent harm. Understanding the definition and scope is crucial for identifying risks and implementing safe practices. This knowledge is essential for both employers and employees to ensure compliance with safety standards and reduce workplace injuries effectively.
Regulations and Legislation Governing Manual Handling
Manual handling activities are governed by specific laws and regulations aimed at reducing workplace injuries. In the UK, the Manual Handling Operations Regulations 1992 require employers to assess manual handling risks and take steps to reduce them. Similar laws exist in other countries, emphasizing employer responsibility to provide safe working conditions. These regulations mandate proper risk assessments, employee training, and the implementation of safe handling techniques. Non-compliance can lead to legal penalties and increased workplace accidents. Understanding these regulations is crucial for employers to ensure adherence and for employees to recognize their rights and responsibilities in maintaining a safe work environment.
Key Techniques for Safe Manual Handling
Safe manual handling techniques are essential to prevent injuries and ensure efficient task completion. Maintaining proper posture, bending at the knees, and lifting close to the body are fundamental practices. Assessing the load’s size, weight, and balance before lifting is crucial. Using leg muscles instead of the back to lift reduces strain. Keeping the object close to the body minimizes the risk of losing control. Avoiding twisting movements and taking regular breaks can prevent fatigue and injury. Team lifting for heavy objects and using mechanical aids when necessary are also recommended. These techniques, when applied consistently, promote a safer working environment and reduce the likelihood of manual handling-related accidents.
Employer Responsibilities in Manual Handling
Employers play a critical role in ensuring safe manual handling practices in the workplace. They must conduct thorough risk assessments to identify potential hazards and implement control measures. Providing adequate training on manual handling techniques, regulations, and equipment usage is essential. Employers are also responsible for ensuring that employees use personal protective equipment (PPE) and mechanical aids when necessary. They must monitor compliance with safety protocols and address any unsafe practices promptly. Additionally, employers should foster an environment where employees feel comfortable reporting injuries or concerns. Regular updates to training programs and policies help maintain a safe and compliant workplace, reducing injury risks and promoting overall well-being.
Employee Responsibilities in Manual Handling
Employees must adhere to manual handling training and guidelines provided by their employer. They are responsible for using proper lifting techniques, wearing required personal protective equipment (PPE), and reporting any hazards or injuries promptly. Employees should avoid lifting loads that exceed their capability and ensure they use mechanical aids when available. They must follow workplace safety protocols and participate in training sessions to stay informed. Employees are also expected to maintain a safe working environment and encourage colleagues to do the same. By taking these steps, employees contribute to reducing manual handling risks and promoting a safer workplace culture overall.
Common Risks and Injuries Associated with Manual Handling
Manual handling poses risks of musculoskeletal disorders, back strains, herniated discs, and sprains. Poor lifting techniques, heavy loads, and repetitive tasks often lead to such injuries, affecting both physical and psychological well-being.
Most Common Injuries from Manual Handling
The most common injuries from manual handling include musculoskeletal disorders, back strains, herniated discs, and sprains. These injuries often result from poor lifting techniques, repetitive tasks, or excessive loads. Back injuries are particularly prevalent due to the spine’s vulnerability during lifting. Additionally, tendon and ligament damage can occur from sudden movements or overexertion. Proper training and adherence to safety guidelines are crucial to minimizing these risks. Employers and employees must prioritize safe practices to prevent long-term physical and psychological impacts associated with manual handling injuries.
Risk Factors for Manual Handling Injuries
Risk factors for manual handling injuries include heavy or awkwardly shaped loads, repetitive tasks, and poor lifting techniques. Environmental factors like slippery surfaces or uneven terrain also increase risks. Individual factors such as physical fitness, prior injuries, and fatigue play a role. Organizational factors, including inadequate training or insufficient recovery time, further contribute. Identifying these risks is crucial for implementing preventive measures and reducing injury likelihood. Employers must assess tasks and provide proper training to mitigate these factors, ensuring a safer workplace for all employees engaged in manual handling activities.
Real-World Case Studies of Manual Handling Accidents
Real-world case studies of manual handling accidents highlight common risks and consequences. For instance, a warehouse worker injured their back while lifting a heavy box without proper support. Another case involved a healthcare employee straining their shoulder due to improper patient lifting techniques. These incidents often result from poor training, ergonomic oversights, or ignoring safety protocols. Analyzing such cases helps identify patterns, such as inadequate equipment use or insufficient team lifting practices. By understanding these real-world examples, organizations can develop targeted training programs to prevent future accidents and improve workplace safety standards, ensuring safer manual handling practices for all employees involved.
Physical and Psychological Impact of Manual Handling Injuries
Manual handling injuries can have severe physical and psychological effects on individuals. Physically, injuries often result in musculoskeletal disorders, back strains, and chronic pain, reducing mobility and work capacity. Psychologically, victims may experience stress, anxiety, and decreased morale due to prolonged recovery periods and potential job insecurity. These impacts extend beyond the individual, affecting team productivity and organizational morale. Employers must address these consequences by implementing preventive measures and providing adequate support to injured employees. Understanding these effects emphasizes the importance of proper training and safe practices to minimize long-term physical and psychological harm in the workplace.
Prevention Strategies for Manual Handling Injuries
Preventing manual handling injuries involves ergonomic assessments, proper training, and using mechanical aids. Regular exercises, correct lifting techniques, and personal protective equipment also reduce risks effectively.
Importance of Manual Handling Training Programs
Manual handling training programs are crucial for reducing workplace injuries and ensuring compliance with safety regulations. They educate employees on proper lifting techniques, risk assessment, and the use of equipment. These programs also foster a safety-first culture, empowering workers to identify hazards and adopt preventive measures. Regular training ensures that employees stay updated on best practices and legal requirements. Additionally, quizzes and assessments within these programs help reinforce learning and identify knowledge gaps. Employers benefit by minimizing injury-related costs and promoting a healthier, more efficient workforce. Effective training programs are essential for safeguarding both employees and employers in manual handling environments.
Ergonomic Adjustments to Reduce Manual Handling Risks
Ergonomic adjustments play a vital role in minimizing manual handling risks by optimizing workspaces and tasks to fit individual capabilities. Adjusting workstation heights, ensuring proper tool design, and reorganizing layouts can significantly reduce physical strain. Implementing mechanical aids, such as lifts or pulleys, further lessens the need for manual effort. Additionally, training employees to recognize ergonomic hazards and adopt correct postures is essential. Regular risk assessments and tailored solutions help prevent injuries and improve efficiency. These adjustments not only protect workers but also align with legal standards, ensuring a safer and more productive environment for all. They are a cornerstone of effective injury prevention strategies.
Use of Mechanical Aids in Manual Handling
Mechanical aids are essential tools for reducing manual handling risks by minimizing physical effort. Devices like hoists, pulleys, and trolleys enable safe load movement, lowering injury risks. Employers should provide suitable equipment based on task requirements, ensuring proper maintenance and training for employees. Mechanical aids not only reduce strain but also improve efficiency and compliance with safety standards. Regular assessments help identify tasks that benefit most from these tools. By integrating mechanical aids into workflows, organizations can significantly reduce manual handling injuries, fostering a safer work environment while meeting legal obligations. Proper training ensures employees use these aids effectively, further enhancing workplace safety and productivity.
Role of Personal Protective Equipment (PPE) in Manual Handling
Personal Protective Equipment (PPE) plays a vital role in manual handling by protecting workers from physical harm. Common PPE includes gloves, back supports, and safety shoes, which reduce the risk of injuries during lifting or moving objects. These items act as a barrier between the worker and potential hazards, such as sharp edges or heavy loads. PPE is particularly crucial in high-risk environments where manual handling is frequent. Employers must ensure suitable PPE is available and that employees are trained in its proper use. While PPE does not eliminate risks, it significantly reduces the likelihood of injury when combined with proper techniques and safety protocols.
Manual Handling Quiz Questions and Answers
This quiz provides multiple-choice and true/false questions to assess knowledge on manual handling principles, techniques, and regulations. It covers lifting practices, injury prevention, and employer responsibilities, ensuring compliance with safety standards and promoting a safer work environment.
Structure and Format of the Quiz
The quiz is designed as a multiple-choice assessment with true/false questions, totaling 10 questions. Each question addresses specific aspects of manual handling, such as proper lifting techniques and employer responsibilities. The format ensures clarity, with one correct answer per question. Topics covered include injury prevention strategies and compliance with safety regulations. The quiz aims to evaluate knowledge retention and understanding of safe manual handling practices. A pass mark of 70% is required, with a 15-minute time limit. This structured approach helps identify knowledge gaps and ensures adherence to legal standards, promoting a safer workplace environment through effective training and assessment.
Types of Questions Included in the Quiz
The quiz includes multiple-choice questions, true/false questions, and scenario-based questions. Multiple-choice questions assess knowledge of specific manual handling principles, such as proper lifting techniques and legal requirements. True/false questions evaluate understanding of common misconceptions, like the safety of two-person lifts. Scenario-based questions present real-world situations, testing the ability to apply safe manual handling practices. Additionally, questions cover topics like the role of PPE, ergonomic adjustments, and employer-employee responsibilities. This variety ensures a comprehensive assessment of knowledge and understanding of manual handling safety, helping to identify gaps in training and promote compliance with regulations.
Sample Questions from the Manual Handling Quiz
The quiz includes a variety of questions to assess knowledge and understanding of manual handling principles. For example:
Which of the following is NOT a safe lifting practice?
a) Lifting with bent knees
b) Keeping the load close to the body
c) Twisting while lifting
True or False: An employer is only required to consider lifting and lowering tasks in manual handling assessments.
These questions cover topics like proper techniques, legal responsibilities, and risk reduction strategies. Additional examples include:
What is the primary purpose of using mechanical aids in manual handling?
and
Which of the following injuries is most commonly associated with poor manual handling practices?
These sample questions demonstrate the quiz’s focus on practical application and regulatory compliance, ensuring a thorough understanding of safe manual handling practices.
How to Interpret Quiz Results for Improved Training
Interpreting quiz results is crucial for enhancing manual handling training effectiveness. Review individual and group scores to identify knowledge gaps and areas requiring additional focus. Analyze which questions were frequently answered incorrectly to pinpoint common misunderstandings. Compare results against compliance standards to ensure legal and safety requirements are met. Use insights to tailor future training sessions, emphasizing topics where participants performed poorly. For example, if many struggled with proper lifting techniques, dedicate more time to practical demonstrations. Track progress over time to measure the impact of training adjustments and ensure continuous improvement in manual handling practices.
Best Practices for Creating Effective Manual Handling Quizzes
When designing manual handling quizzes, ensure questions are clear, concise, and directly related to real-world scenarios. Include a mix of multiple-choice and true/false questions to keep participants engaged. Cover key topics like proper lifting techniques, employer responsibilities, and injury prevention. Align questions with legal and safety regulations to reinforce compliance. Provide immediate feedback with correct answers and explanations to enhance learning. Regularly update questions to reflect new guidelines or common challenges. finally, ensure the quiz is accessible in formats like PDF for easy distribution and completion, making it a practical tool for both trainers and participants.
Legal and Compliance Aspects of Manual Handling
This section outlines the legal obligations and compliance requirements for manual handling, ensuring adherence to workplace safety regulations and employer responsibilities.
Overview of Manual Handling Laws and Regulations
Manual handling laws and regulations are designed to protect workers from injuries caused by lifting, carrying, or moving objects. In many countries, these laws require employers to assess manual handling risks and implement safe practices. For example, the Manual Handling Operations Regulations 1992 in the UK mandates employers to avoid manual handling where possible and reduce risks through proper training and equipment. Similar regulations exist globally, emphasizing employer responsibilities to provide safe working conditions. These laws often include guidelines on weight limits, proper lifting techniques, and the use of mechanical aids. Compliance is crucial to prevent injuries and legal penalties.
Consequences of Non-Compliance with Manual Handling Regulations
Non-compliance with manual handling regulations can result in severe legal and financial penalties for employers. Fines and legal actions are common outcomes for failing to adhere to safety standards. Additionally, workplaces may face reputational damage, losing client trust and business relationships. Employees may suffer injuries, leading to workers’ compensation claims and increased healthcare costs. Non-compliance can also disrupt operations, as investigations and legal proceedings divert resources. Furthermore, organizations may experience reduced productivity due to injured workers and the need to retrain staff. Ultimately, non-compliance jeopardizes workplace safety and can lead to long-term financial and operational challenges for the organization.
Ensuring Quiz Content Meets Legal Standards
Ensuring quiz content meets legal standards is crucial for compliance with health and safety regulations. Quizzes must align with laws such as the Health and Safety at Work Act and the Manual Handling Operations Regulations. Questions should cover key legal requirements, including risk assessments, employer responsibilities, and employee training obligations. The content must be accurate, up-to-date, and relevant to workplace scenarios. Regular updates are necessary to reflect changes in legislation. Additionally, quizzes should be designed to test knowledge of legal duties, such as proper lifting techniques and the use of personal protective equipment. This ensures that both employers and employees remain legally compliant and informed.
Best Practices for Using Manual Handling Quizzes
Integrate quizzes into training programs to reinforce learning, encourage active participation, and ensure consistent understanding of safe manual handling practices across all employees.
Integrating Quizzes into Overall Training Programs
Quizzes are a valuable tool for reinforcing manual handling training. They should be incorporated into broader training programs to assess understanding and identify knowledge gaps. By using quizzes, employers can ensure employees grasp key concepts, such as proper lifting techniques and safety protocols. Regular testing helps maintain engagement and retention of critical information. Quizzes also provide immediate feedback, allowing for targeted follow-up training. Integrating quizzes into overall programs ensures a comprehensive approach to manual handling education, promoting a culture of safety and compliance in the workplace. This method supports continuous improvement and helps reduce the risk of injuries and non-compliance with regulations.
Encouraging Active Participation in Manual Handling Training
Active participation in manual handling training is crucial for ensuring employees fully understand and apply safe practices. Engaging activities such as group discussions, hands-on exercises, and real-life scenario simulations can foster involvement. Providing immediate feedback through quizzes and assessments helps reinforce learning. Encouraging employees to ask questions and share experiences creates a collaborative environment. Recognizing and rewarding contributions can also motivate individuals to take an active role. By making training interactive and relevant, employers can ensure that employees are invested in their own safety and the safety of others, leading to a more effective and sustainable learning experience in the workplace.
Continuous Improvement of Manual Handling Quiz Content
Continuous improvement of manual handling quiz content ensures it remains relevant and effective. Regular updates align with changing regulations and new techniques. Incorporating feedback from participants and trainers helps refine questions for better clarity and engagement. Adding real-life case studies and scenario-based questions enhances practical understanding. Aligning quiz content with current training programs and legal standards maintains compliance. Periodic reviews of quiz results identify knowledge gaps, enabling targeted improvements. By fostering a culture of ongoing enhancement, organizations ensure their manual handling training remains impactful and up-to-date, ultimately reducing risks and promoting a safer workplace environment.
The manual handling quiz questions and answers PDF is a vital resource for enhancing safety and compliance. It provides a practical tool for testing knowledge and understanding, ensuring a safer workplace by promoting proper techniques and legal adherence.
The manual handling quiz questions and answers PDF serves as an essential resource for enhancing understanding and compliance. It covers critical areas such as proper lifting techniques, employer responsibilities, and injury prevention strategies. The quizzes are designed to assess knowledge retention and ensure adherence to safety regulations. By incorporating multiple-choice and true/false questions, the resource engages learners effectively. It also provides a practical tool for identifying gaps in training and improving workplace safety. Regular use of these quizzes can significantly reduce manual handling risks and foster a culture of safety within organizations. This makes it a valuable asset for both employees and employers alike.
Final Thoughts on the Importance of Manual Handling Training
Manual handling training is crucial for ensuring workplace safety and preventing injuries. The use of quizzes with questions and answers provides an engaging and effective way to reinforce learning and assess understanding. By covering topics like proper lifting techniques, employer responsibilities, and injury prevention, these resources help create a culture of safety. Regular engagement with such materials fosters continuous improvement and compliance with regulations. Ultimately, investing in manual handling training not only protects employees but also reduces organizational risks, making it a vital component of any workplace safety program. Its impact extends beyond individual knowledge, contributing to a safer and more responsible work environment.